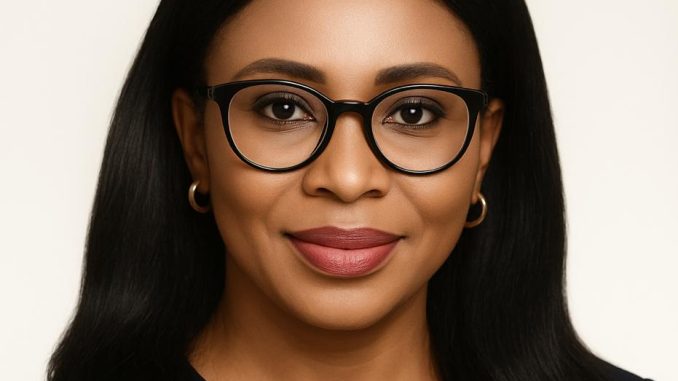
Despite the consistent market demand for essential goods, Nigerian manufacturers face significant power challenges.
However, transitioning from the unstable grid supply to gas plants, is helping manufacturers reduce the cost of doing business.
Executive director at Kitchen Vegetable Oil, Ifeyinwa C. Udeagbala, said the high cost of grid power and the instability of the electricity supply, which poses a risk to their factory equipment, influenced the company’s decision to switch to gas plants, relying only on diesel gensets as a backup.
The company, Kitchen Vegetable Oil Limited, a subsidiary of Udeagbala Holdings, a manufacturer and marketer of FMCG and industrial goods, including skincare brands, edible oils, multipurpose soaps and PVC pipes for home and industrial use, made the switch two years ago. It is based in Aba, Abia state.
To tackle its power challenges, the company partnered with Clarke Energy to integrate a 1.7 megawatt (MW) Jenbacher gas plant, sourcing pipeline gas from one of Nigeria’s foremost IOC downstream subsidiaries and compressed natural gas (CNG) from virtual pipeline suppliers.
Clarke Energy provided the front-end engineering designs, supplied the gensets, commissioned the plant, and currently provides after-sales services.
“The gas plant is generating cleaner electricity and significantly reducing our operational costs compared to diesel,” Udeagbala said. “It has addressed efficiency issues, making our operations more sustainable.”
Yiannis Tsantilas, Managing Director of Clarke Energy for sub-Saharan Africa, emphasised the importance of sustainable and cost-effective energy solutions for manufacturers.
“Globally, the availability of raw materials and reliable and affordable energy are important drivers in industrialising any economy. In Nigeria, many manufacturers experience these challenges, especially the issues of irregular grid supply and high energy costs, which constitute almost 40 per cent of their expenses,” said Tsantilas, citing data from the Manufacturers Association of Nigeria (MAN).
“The visionary leadership at Kitchen Vegetable Oil Limited recognised the need to utilise available gas as an alternative fuel, allowing them to self-generate a more sustainable power supply to lower their cost per product and increase their competitiveness in the market,” he added.
Udeagbala said the manufacturing challenges are multifaceted, “The challenge is not just about meeting market standards; it is about navigating the economic and logistical barriers that make production and distribution difficult.”
These include inflation, fluctuating raw material costs, low purchasing power of consumers, and limited access to affordable capital, which hamper business expansion.
“For a business like ours, which requires heavy upfront investment in raw materials, equipment, and labour, we need more sustainable bank interest rates. The high cost of borrowing erodes profit margins, making growth challenging,” she said.
The prevalence of counterfeit industrial materials and difficulty in sourcing spare parts, often imported with long delays and high costs, adds to operational challenges.
Nigeria’s complex tax environment, with multiple agencies imposing levies, adds another layer of burden. While some states have streamlined processes, inconsistencies and the overall tax burden, including VAT, corporate tax, and import duties, strain already thin margins.
Despite these hurdles, Udeagbala expressed a commitment to continuing operations, driven by a sense of legacy and responsibility toward employees. The company, with over 200 employees, views job creation and stability as essential, particularly considering Nigeria’s high unemployment rate.
She said the company has plans to expand into neighbouring African markets. “We are reviewing regional economic policies and how to scale borders complexities: delays at checkpoints and the risks associated with transporting perishable goods,” Udeagbala said.
Udeagbala said their success had been due to their employees’ resilience, prioritising raw material quality, long-term relationships with trusted suppliers and service providers, and rigorous testing protocols to maintain product quality. The company said it has rejected shipments of substandard materials to protect product quality and equipment.